
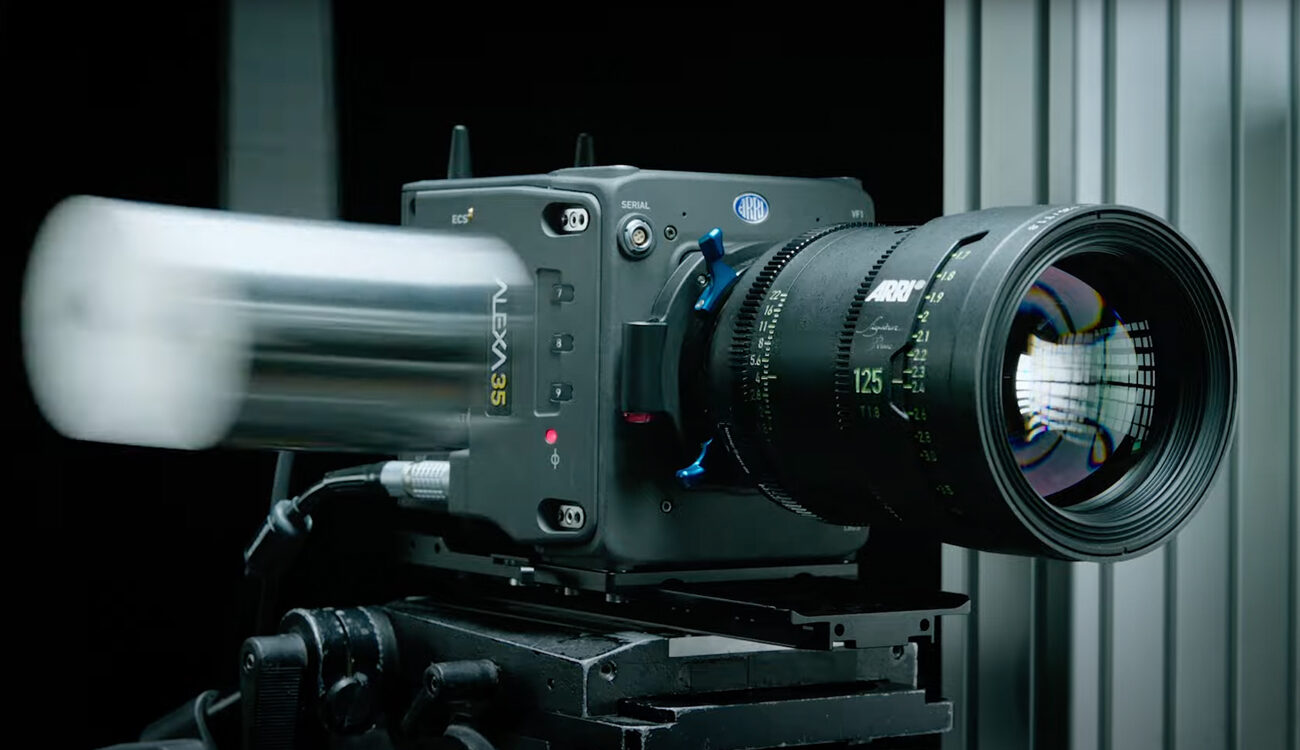
ARRI has recently released a short video showcasing the strict test procedures that their new Super 35 flagship model, the ALEXA 35, had to undergo during development. The camera body can resist extreme temperatures and impacts, while still providing protection against scratches, splashes, and dust. Let’s take a closer look.
Crash tests have always been an opportunity for car companies to impress customers by showing them how safe and reliable their vehicles are. That’s because you not only want a car that is fast, reactive, and performing. You want a car that brings you home safely in the first place.
Although in a much lighter way, the same concept applies to investing in a digital camera system. At the end of the day, ultra-high-resolution, skyrocketing frame rates, and higher-than-the-human-eye dynamic range mean nothing if packed into a body that cannot face the unexpected. So before you go on reading, take 30 seconds to watch the following “ARRI ALEXA 35 – Durability Test” video.
ARRI ALEXA 35: built to last
There’s pretty much no doubt that the newly-released ARRI ALEXA 35 will set a new milestone in the realm of digital cinematography. In case you’re among the few people that missed my colleague Nino’s in-depth interview with ARRI about the new camera, make sure to watch it here.
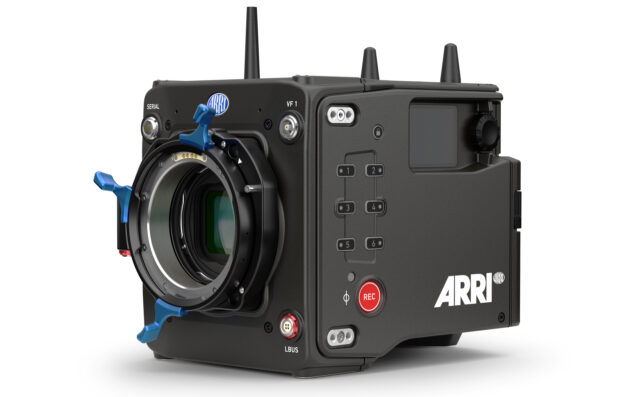
Sure, its new 4.6K 3:2 Super 35 sensor, 19 recording formats, 17 claimed stops of dynamic range, REVEAL Color Science, and ARRI Textures are features that truly matter to cinematographers, who explicitly asked for them. However, there’s much more to this list of specs.
Indeed, as the video clearly shows, the company put all their 100+ years of expertise into developing a camera that is (truly) built like a tank. Indeed, unlike the carbon fiber ALEXA Mini, the ALEXA 35 body has a solid metal construction with individually replaceable panels.
ARRI ALEXA 35: durability test
Throughout the development process, the ALEXA 35 was stress-tested in unimaginable ways. It has been shaken like a leaf in a hurricane, exposed to red heat (45°C) as well as freezing cold temperatures (-20°), and put under the pressure of strong impacts. And still, it survived all these challenges.
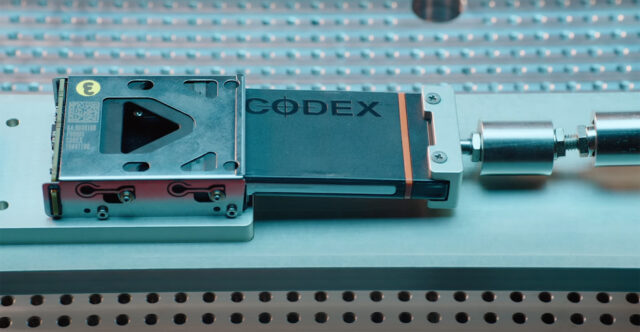
Moreover, the company relies on robotics to repeatedly test all parts that are more likely to incur wear and tear due to intense usage on set. These include the media card slot and all sorts of power, video, and auxiliary connectors.
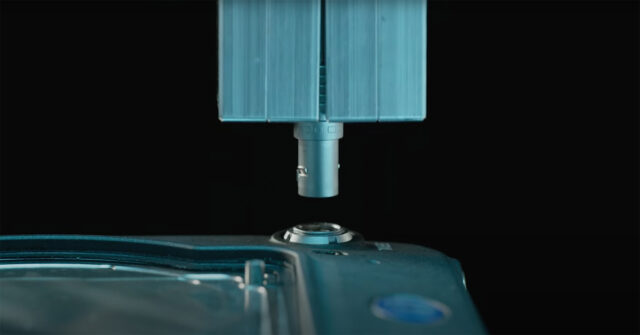
Finally, ARRI carries out premium quality controls by putting each ARRI ALEXA 35 unit through a series of temperature and vibration tests before shipping the camera out. So when you finally unbox it, you won’t need to second-guess your €60.000+ investment.
How much does reliability matter to you when investing in a new camera system? What do you think about the ARRI ALEXA 35 durability test? Let us know your thoughts in the comment section below!